Hablar de fabricación aditiva en el sector de la automoción ya no suena a promesa de futuro, sino a una realidad bien implantada desde hace años. Desde los primeros esfuerzos de los ingenieros para fabricar utillaje con impresión 3D FFF con filamento PLA hasta la fabricación de precisas piezas en resina para el interior de vehículos, el prototipado funcional con refuerzo interno de fibra o el desarrollo avanzadas soluciones de fabricación de pre-series o series cortas en PP, el avance en los últimos tiempos ha sido muy grande.
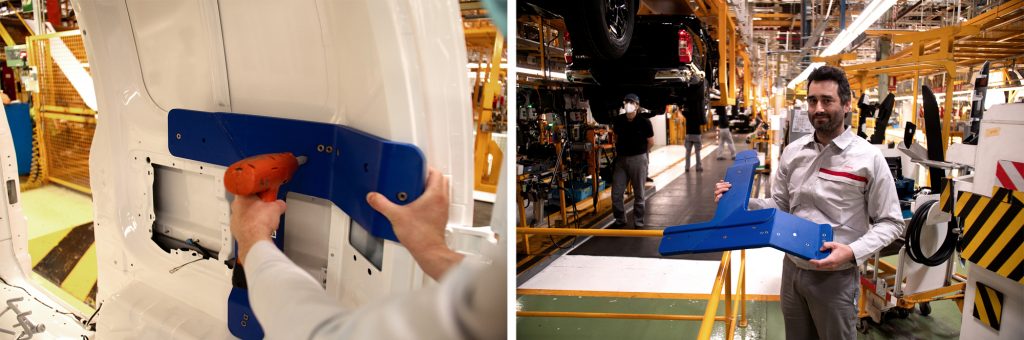
La fabricación de utillaje con impresoras 3D de extrusión de plástico se sigue mostrando, no obstante, como el modo más accesible y rápido de obtener un rápido retorno de la inversión en una planta industrial de este tipo. Los materiales de construcción suelen ser económicos y fáciles de trabajar (sobre todo si se opta de primeras por el PLA, para piezas que no requieran grandes esfuerzos), y la diferencia de costes y de tiempos en comparación con la subcontratación de estos servicios a proveedores externos justifica por sí sola en poco tiempo la introducción de las impresoras en el flujo de trabajo de la empresa.
Empresas punteras en el sector de la extrusión de plástico han mostrado al público ejemplos muy representativos con grandes marcas del sector automovilístico. La más reciente ha sido BCN3D, cuya implantación en la fábrica de Nissan en Barcelona ha permitido conseguir en un solo día procesos que antes se demoraban semanas, y con costes hasta 20 veces más bajos.
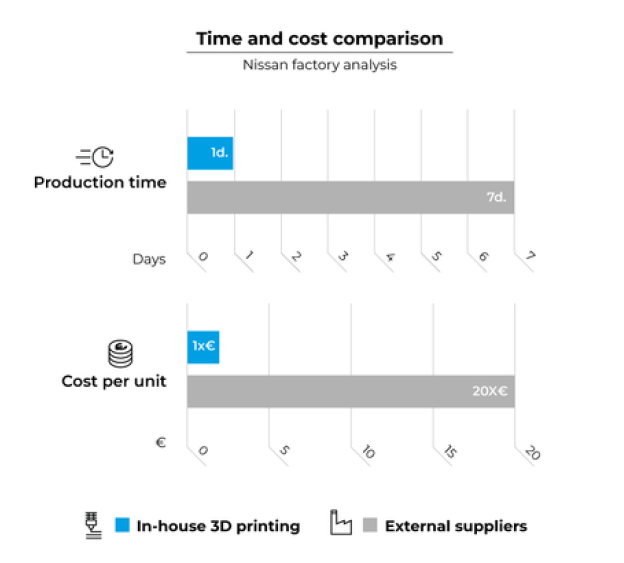
«Cuando empezamos en 2014, para la primera herramienta sencilla que queríamos imprimir nos presupuestaron costes de unos 400€ por el mecanizado. En su lugar, lo hicimos aquí en nuestra fábrica y tras fabricar 3 herramientas ya habíamos amortizado la máquina.»
– Enric Ridao, Ingeniero Kaizen de Fabricación de Tapicerías y Chasis de Nissan Motor Ibérica Zona Franca, Barcelona.
Ejemplo: Galga centradora de parabrisas
Tecnología | BCN3D |
Material | TPU |
Tiempos | 14 h |
Coste | 8 € |
Tamaño | 100 x 120 x 80 mm |
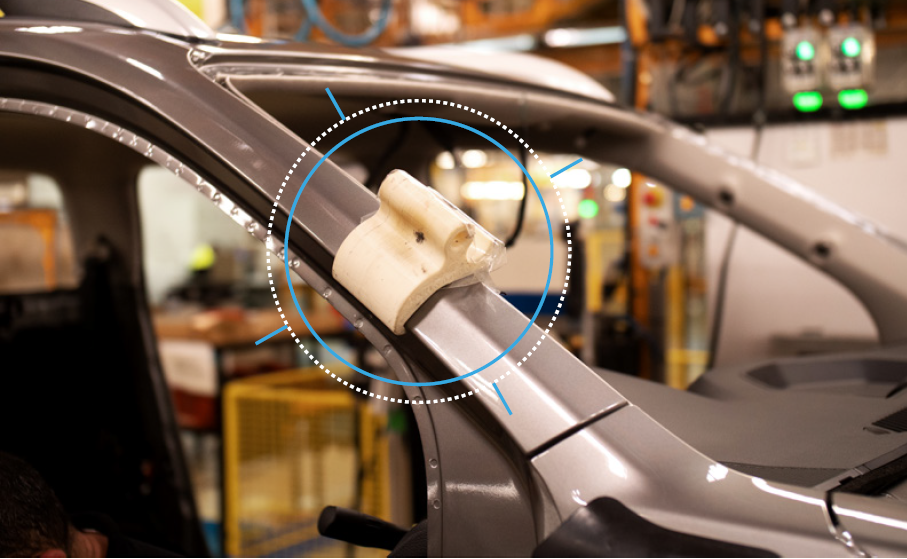
Ultimaker en Volkswagen Autoeuropa
En el caso de Ultimaker tenemos el caso de éxito de la fabrica de Volkswagen Auroeuropa en Portugal, cuyos ejemplos mostraron en su momento un camino a seguir a otras industrias similares. El éxito de la implantación de las impresoras 3D en esta planta fue tal que casi la totalidad de sus herramientas (93%) ahora se producen localmente en lugar de ser encargadas a proveedores externos. Otra ventaja es que les permitía probar soluciones de forma casi inmediata, sin tener que contactar con terceros simplemente para probar la geometría de un prototipo. De ese modo el tiempo medio de obtención de estos componentes se redujo de media unas ocho semanas.
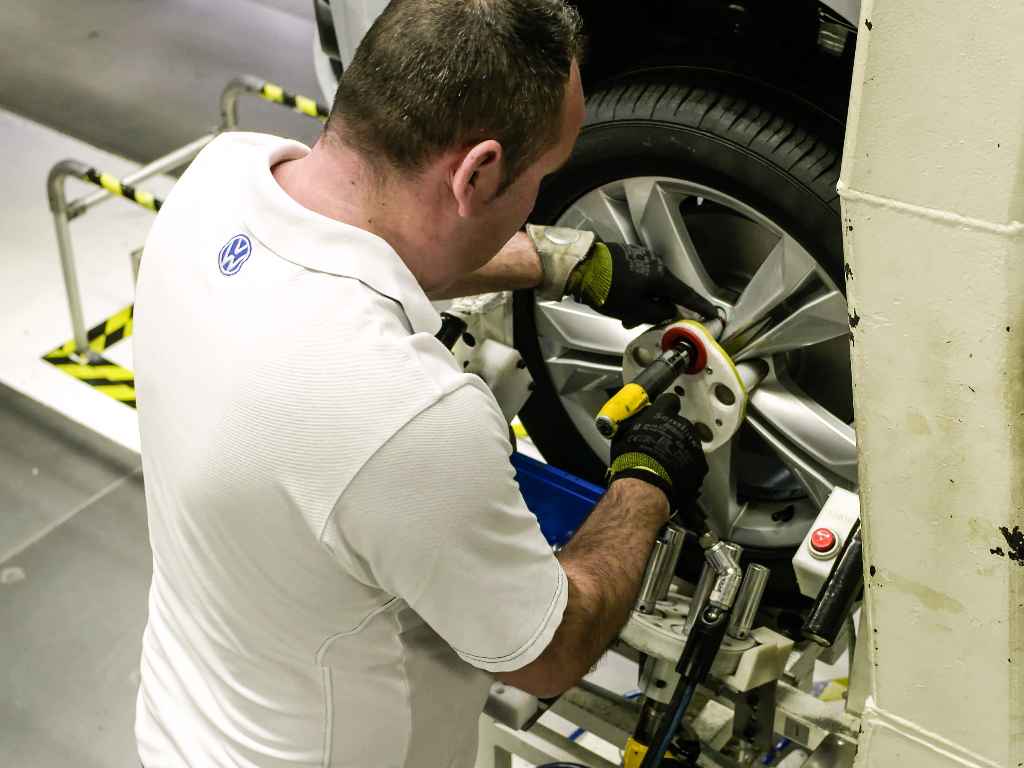
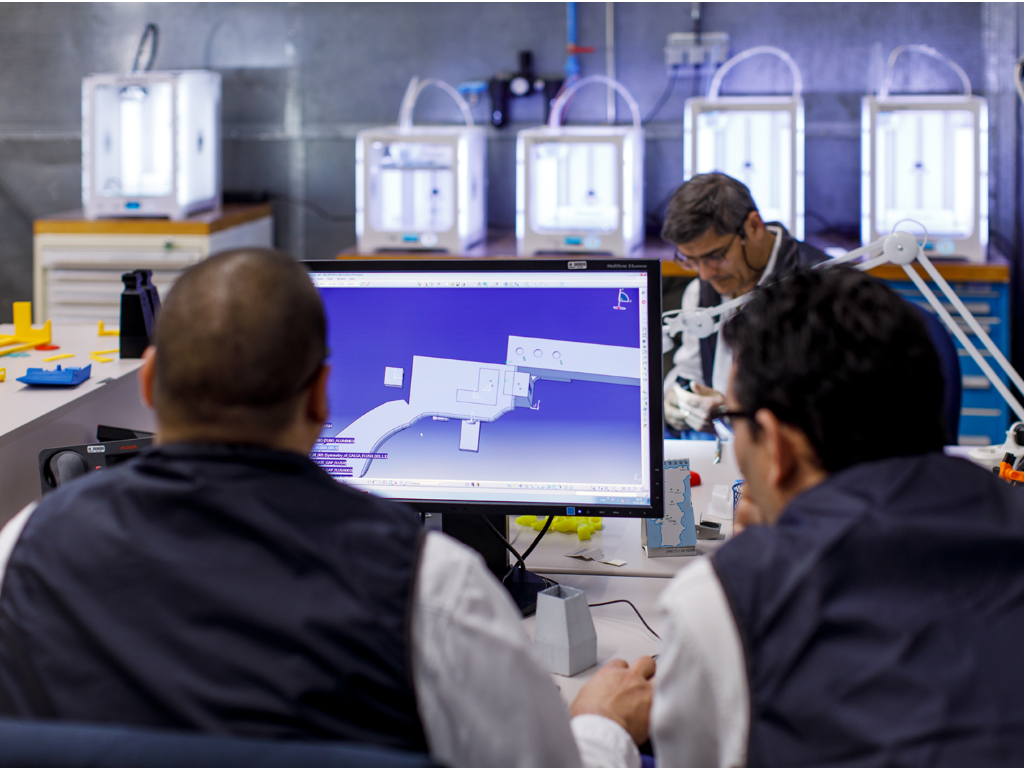
Las impresoras 3D con la tecnología 3D de Ultimaker permitieron a Volkswagen Autoeuropa fabricar piezas con diseños complejos, desarrollar ideas y fabricarlas en el mismo día y reducir drásticamente costes y tiempos de entrega, al no tener que fabricar distintos moldes para obtener las piezas deseadas y probar iteraciones de diseño.
Ejemplo: Posicionador de portón trasero
Tecnología | Ultimaker |
Coste externalizado | 400 € |
Tiempo externalizado | 35 días |
Coste in-house | 10 € |
Tiempo in-house | 4 días |
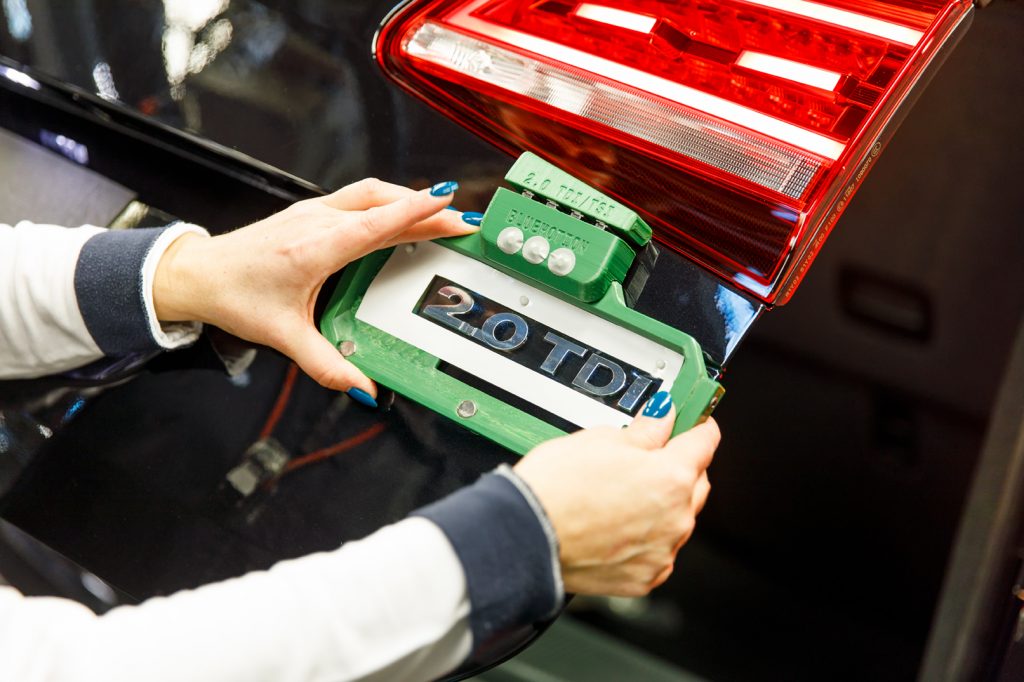
Mediante la fabricación de prototipos in-house Volkswagen Autoeuropa llegó a una reducción de costes del 91%, equivalente a 150.000 € al año, y a una reducción de tiempos de entrega entre un 40% y un 90%.