DESCRIPCIÓN
La empresa Smart Materials 3D sufre una rotura en uno de los acoples metálicos de la bobinadora de filamento plástico para impresión 3D. La rotura es debida a una caída del acople al suelo, realizando una abolladura en la parte cónica de ajuste al carrete de bobinado. Desde este momento la bobinadora no se puede poner en marcha debido a que no se puede realizar el ajuste y apriete de los carretes contra los ejes de bobinado.
PROBLEMATICA DE LA SITUACIÓN INICIAL
- La línea de producción no se puede poner en marcha hasta no disponer de un nuevo ajuste cónico, ya que el filamento no se puede bobinar en los carretes.
- Se solicita presupuesto a una empresa de mecanizado para que realice una pieza similar, informando de un coste de 575 € y 2 semanas de plazo de entrega.
- Aunque se realizase el encargo a la empresa de mecanizado (asumiendo 2 semanas de parada de producción) seguiría existiendo el mismo riesgo de caída y deformación de la pieza, ya que es una pieza que se acopla y desacopla aproximadamente cada 5 minutos en la máquina, con cada cambio de bobina.
- La pieza actual dispone de un único diseño en tamaño por lo que solo es útil para un único tamaño de carrete, hay que disponer de un conjunto de piezas para toda la gama de carretes que admite la línea.
FASES DE LA PROPUESTA DE SOLUCIONES
- Smart Materials se puso en contacto con Grupo Sicnova, fabricante de la impresora 3D Sicnova JCR 1000, para hacer un diseño mejorado de la pieza, de forma que fuese universal y adaptable a todos los tamaños de carretes disponibles en la empresa.
- De una fase inicial de diseño se pasó a la fabricación aditiva de la pieza en cuestión, debido a la reducción de tiempos en su construcción, en comparación con el mecanizado tradicional.
- Como material base en su fabricación se estudió la incorporación del poliestireno especial que soporta altos impactos y por lo tanto posibles caídas de la pieza en su manipulación.
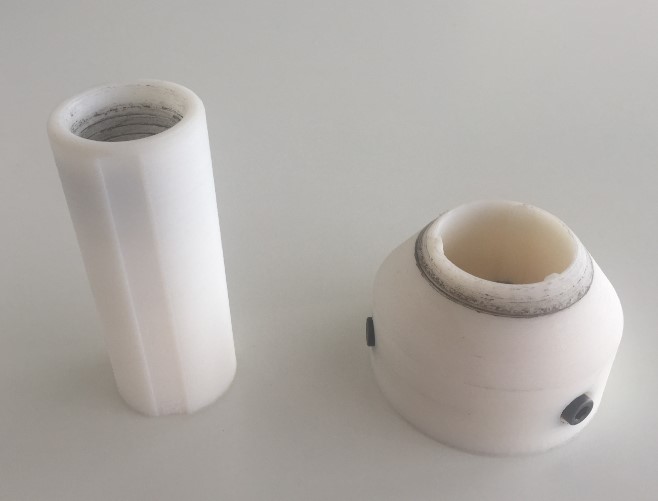
I+D+i DEL CASO
Gracias a la colaboración con Gupo Sicnova se han seguido las siguientes fases en la resolución del caso:
- Diseño de una pieza mejorada, universal y adaptable a cualquier tipo de carrete usado la línea de producción de Smart Materials, siendo ajustable en diámetro y longitud.
- Utilización de la impresora 3D Sicnova JCR 1000 para la impresión de las dos partes del conjunto de la pieza, con un acabado excepcional y un ajuste perfecto en el roscado, centrado y apriete.
- Utilización de material de impresión desarrollado para que la pieza soporte los impactos y choques sin deformarse ni romperse.
REPERCUSIÓN EN EL CLIENTE
- Ahorro en más de un 96% en costes. 18,3 € frente a los 575 € del mecanizado tradicional.
- Ahorro de un 100% en inversiones, ya que no se necesitan piezas de repuesto para futuras posibles roturas.
- Ahorro en más de un 77 % de tiempo de espera. 8 horas de impresión en la JCR 1000 frente a las 2 semanas de plazo de entrega del mecanizado.
- Ahorro en un 60% en número de útiles, al mejorar el diseño y hacerlo adaptable a todos los modelos de carretes.
RESULTADOS OBTENIDOS
Desde Smart Materials se aseguran y garantizan los resultados obtenidos y descritos desde el día 28 de abril de 2015, en que se implantó el presente caso de éxito.