Sicnova y la Maestranza Aérea de Madrid (MAESMA), perteneciente al Ejército del Aire Español, han trabajado codo con codo para el desarrollo de aplicaciones de impresión 3D usando la tecnología de Markforged. Algunas de las aplicaciones más destacadas pueden verse en el siguiente vídeo, grabado recientemente en las instalaciones que esta institución tiene en la base aérea de Cuatro Vientos.
La Maestranza Aérea de Madrid es un órgano perteneciente al Ejército del Aire Español, encargado del mantenimiento de su flota aérea . En concreto, trabajan habitualmente en la revisión y puesta a punto de los helicópteros Super Puma y Cougar, así como de los aviones C212 y C235. Desde hace varios años en el departamento de ingeniería de MAESMA existía un interés por incorporar la fabricación aditiva a los procesos de trabajo habituales, aunque los primeros intentos con kits de impresión 3D DIY no fueron fructíferos. El asesoramiento de Sicnova ha sido clave para que la institución profesionalice el uso de la fabricación aditiva, en concreto utilizando la impresora Mark Two de Markforged.
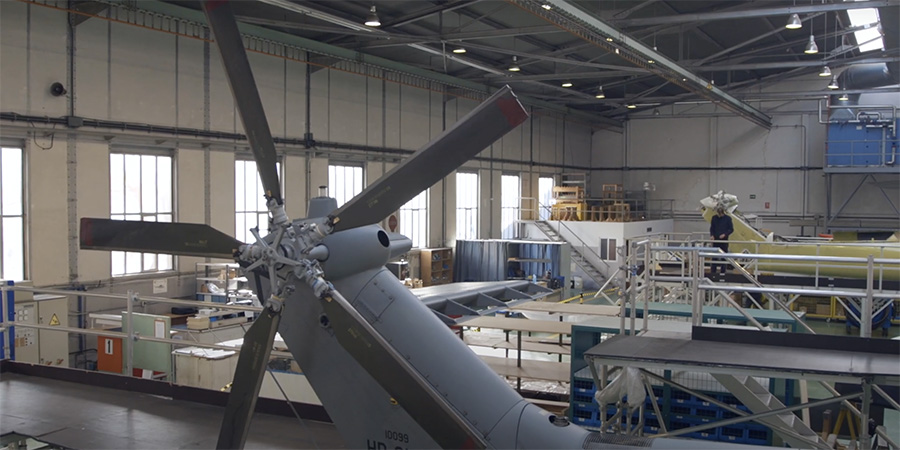
Piezas fabricadas en Maestranza Aérea de Madrid
Gracias a las excelentes propiedades de dureza, resistencia y ligereza de las piezas fabricadas con refuerzo interno de fibra se han desarrollado diversas piezas de utillaje y piezas finales, capaces de soportar las exigentes condiciones de rendimiento necesarias en un contexto donde las tensiones que soportan los componentes son muy altas, y donde no puede caber margen de error.
El capitán Alejandro Aracil, jefe del taller de helicópteros de la MAESMA, afirma que en la actualidad, para cada necesidad de pieza, ya se valora siempre hacerla con fabricación aditiva y evitar la fabricación tradicional. “La tecnología de este tipo de fabricación aditiva en la Maestranza Aérea de Madrid es básicamente el futuro”, señala.
Entre el utillaje fabricado en los últimos meses en MAESMA destacan algunas piezas en concreto, como un utillaje de medición de control de fugas en el tren de aterrizaje del helicóptero, que permite discriminar si una fuga es aceptable o no. Este útil permite ahorrar una media de 25 horas de trabajo por persona, al evitar tener que desmontar el tren para hacer esta comprobación. Al año, esto supone un ahorro de 200 horas por persona, y aproximadamente 10.000 €.
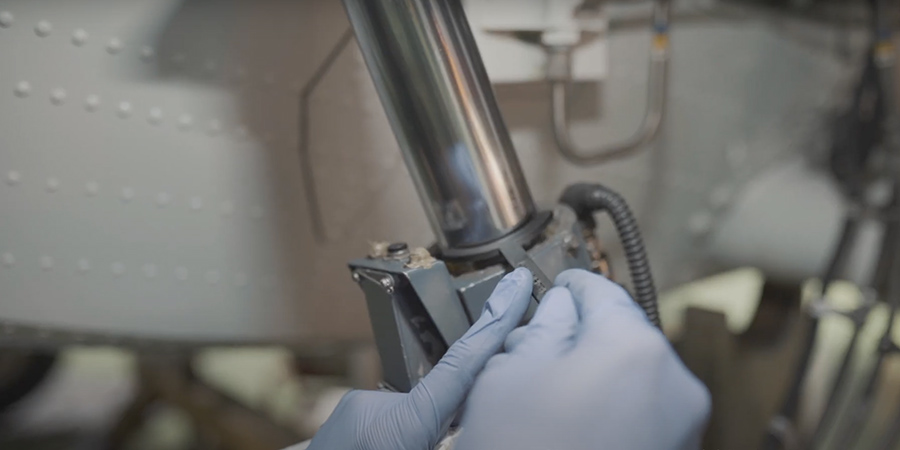
Otra herramienta que ejemplifica bien la utilización de la fabricación aditiva en MAESMA es una llave personalizada para el rotor principal del helicóptero, que permite dar un torque que no era posible hacer con la llave original.
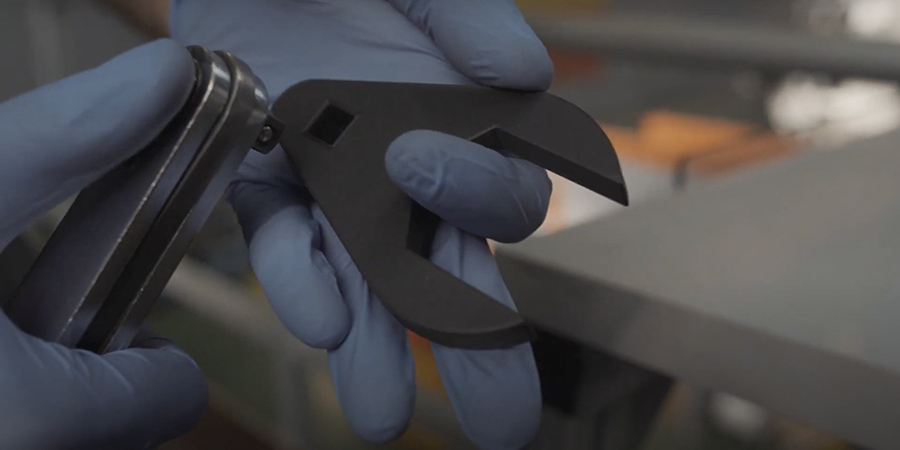
Ambas piezas han sido fabricadas con Onyx, un material que destaca por incluir micro partículas de carbono en su composición, que le otorgan una especial dureza y resistencia.
En el apartado de pieza final, destaca una pieza realizada con Onyx y Kevlar, un protector para la grúa de aterrizaje de un helicóptero Super Puma, que además de un considerable ahorro en el coste de la pieza, permite tener una disponibilidad casi inmediata de la misma y adaptar el diseño a las particularidades de cada modelo de helicóptero.
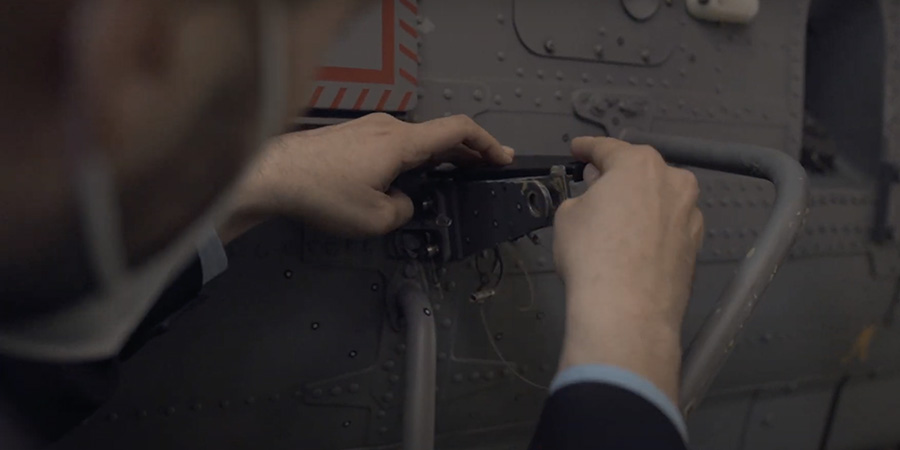
Actualmente el departamento de Ingeniería de la Maestranza Aérea de Madrid continúa con el desarrollo de nuevas piezas utilizando tanto impresoras 3D como escáneres 3D, con el asesoramiento técnico de los especialistas de Sicnova.