Vulcanized Rubber Molding with 3D Printed Masters
Sector
Aplicación
Equipo usado
Vulcanized rubber molds are used to produce wax masters in quantity for investment casting of metal parts such as jewelry, small industrial components, and gaming miniatures.
This process can be beneficial when you want to produce multiples of the same model, retain the design for archival purposes, or want to direct cast from a wax part rather than a directly printed photopolymer.
While Formlabs does offer a Castable Resin for direct investment casting, using vulcanization allows you to create a mold capable of producing multiple copies of wax models for a faster and easier burnout process.
Formlabs tested the compatibility of directly printed master models for vulcanization in Black Resin and High Temp Resin, with room temperature and high temperature molding rubbers. The results indicate that master models printed with the Form 2 are suitable for room temperature vulcanization (RTV) and vulcanization of high temp natural rubber.
1. INTRODUCTION
Vulcanized rubber molds are used to produce wax masters in quantity for investment casting of metal parts such as jewelry, small industrial components, and gaming miniatures. During the chemical process of vulcanization, rubber, which is stringy and weak in its natural state, becomes firmer and tear-resistant. Both natural rubber and silicone can be vulcanized.
Natural rubber and most silicone molding materials vulcanize when exposed to high temperature and pressure. This method, traditionally used by professional jewelers, requires an investment in specialized heat vulcanizing equipment. A wide variety of materials with different hardnesses is available. Some silicone molding rubbers cure at room temperature with the addition of a chemical catalyst; this is called room temperature vulcanization (RTV) or cold molding.
This technique requires a much lower upfront investment, but ongoing material costs may be higher. RTV molds can require anywhere from one hour to eighteen hours to cure. Molds are generally a little firmer than natural rubber or heat-vulcanized silicone. Masters for moldmaking are traditionally machined out of metal (which is expensive and cost prohibitive for small-scale production) or hand-crafted (which may not be precise enough for some applications).
3D printing presents a low-cost method for producing precise CAM master models for vulcanized rubber molds.
Note: RTV can be an attractive technique for small scale production, requiring less initial investment than a heat vulcanizing setup. For a small shop, this makes moldmaking a very reasonablypriced addition to your workflow. There are a wide range of mold materials available. Products such as Castaldo ICE RTV cure within 60 – 90 minutes or less, which can be very quick and convenient.
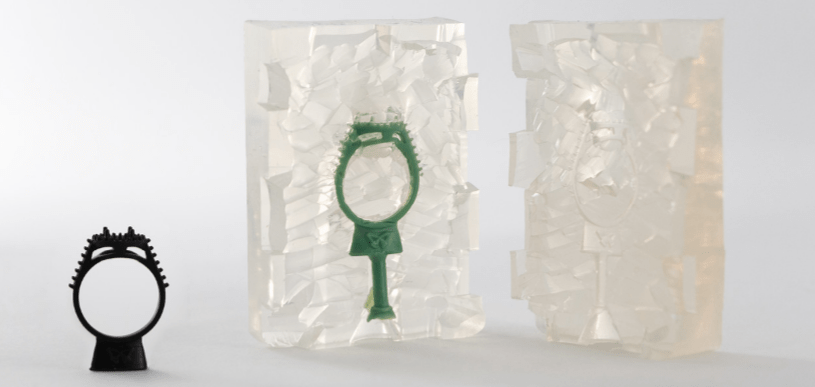
2. TESTING COMPATIBILITY OF MASTER MATERIALS AND MOLDING MATERIALS
We conducted an experiment to determine which rubber molding materials achieved the best results with masters 3D printed with Formlabs Black Resin, a general-purpose prototyping resin with high detail and accuracy, and High Temp Resin, a high-performance engineering resin with a heat deflection temperature (HDT) of 289 °C at 0.45 MPa.
3. METHOD
Several copies of a simple halo ring were printed on a Form 2 stereolithography (SLA) 3D printer in both Black and High Temp Resin at 25 microns. After printing, we washed the models for 20 minutes in a solution of 99% isopropyl alcohol (IPA), allowed them to air dry, and post-cured them for 4 hours under a 365 nm UV lamp.
Formlabs partnered with Alan Leavitt Jewelers in Boston, MA to pack, vulcanize, cut, and assess the molds. After post-curing, we coated the models with a generic mold release and packed them with uncured rubber or silicone. The room temperature silicone molds cured for 18 hours and the high temperature natural rubber molds were vulcanized with heat and pressure. After vulcanization, we cut the molds open with a stepped process to create interlocking geometries and keys that aid in repositioning the two halves of the mold.
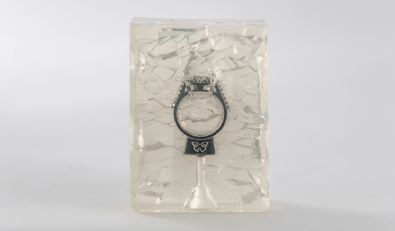
4. RESULTS: ROOM TEMPERATURE VULCANIZING (RTV) SILICONE
Smooth-On SORTA-Clear 40 silicone, which cures at room temperature (21 °C or 70 ˚F), yielded successful molds with both Black and High Temp Resins. Neither master model cracked or changed shape during vulcanization. The Black Resin was easy to see through the clear mold material, so the jeweler could cut the mold quickly and confidently.
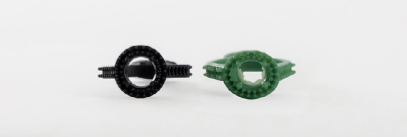
5. RESULTS: HIGH TEMPERATURE NATURAL RUBBER
A mixture of Romanoff Blue Lo-Shrink Rubber and Castaldo Gold Label natural rubber, which cure at 155 °C (310 °F) and 153 °C (307 °F), respectively, yielded a successful mold with High Temp Resin, but not with Black Resin. The High Temp master remained geometrically accurate during and after vulcanization, and the mold rendered each detail with clarity.
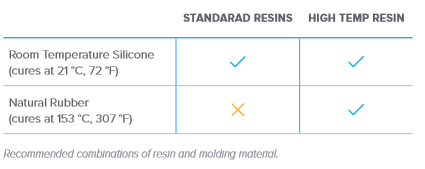
CONCLUSION / RECOMMENDATIONS
Formlabs Standard Black Resin and High Temp Resin can both be used to make vulcanized rubber molds. Black Resin works well for room temperature “cold molding” with silicone and produced a successful mold. Its visibility during cutting simplified the process.
High Temp Resin also works for cold molding, but doesn’t offer the same convenient visibility.
Other Formlabs Standard Resins – Grey, White, and Clear – are mechanically similar to Black Resin and can also be used for room temperature moldmaking. Grey Resin is the most precise Formlabs Standard Resin.
Dental Model Resin, the most precise of all Formlabs resins, is also suitable for room temperature moldmaking. Castable Resin can also be used for RTV processes. This can be useful to jewelers already working with this material. Castable Resin prints are softer than our Standard Resins and so post-curing is required before using Castable prints as master models.
After creating the RTV mold, Castable master models should be inspected for any deformation to confirm the integrity of the mold. Castable Resin would not be suitable for high temperature vulcanization.
High Temp Resin works well for high temperature vulcanization and can be used with natural rubber. High temperature molding silicones may have different mechanical behaviors.
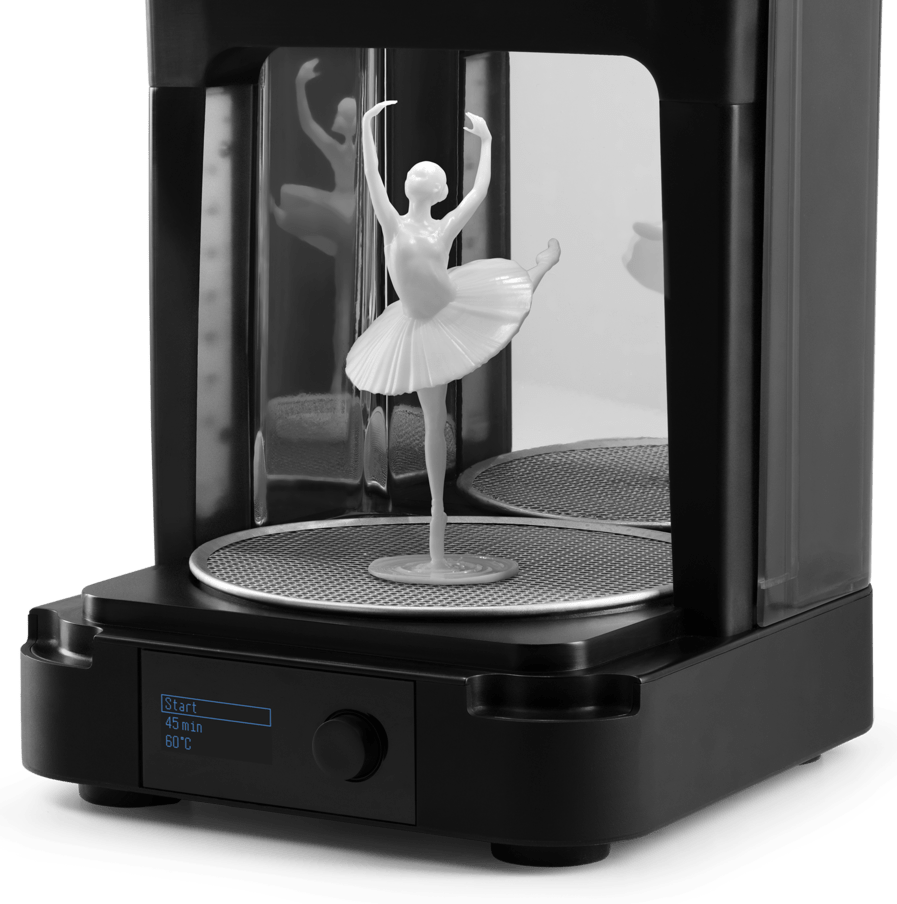
Conoce el equipo utilizado en este caso de éxito.
Form Cure is designed and extensively tested to achieve optimal post-curing for Formlabs resins, providing a reliable, professional post-curing solution. Using settings unique to each material, Form Cure combines the power of 405 nm light with precise temperature control to perfectly post-cure every part.
Otros casos de éxito de Formlabs

Descubre las impresoras 3D de Formlabs: Form 4L y Form 4BL
Formlabs ha revolucionado el mercado de la impresión 3D con la introducción de sus modelos
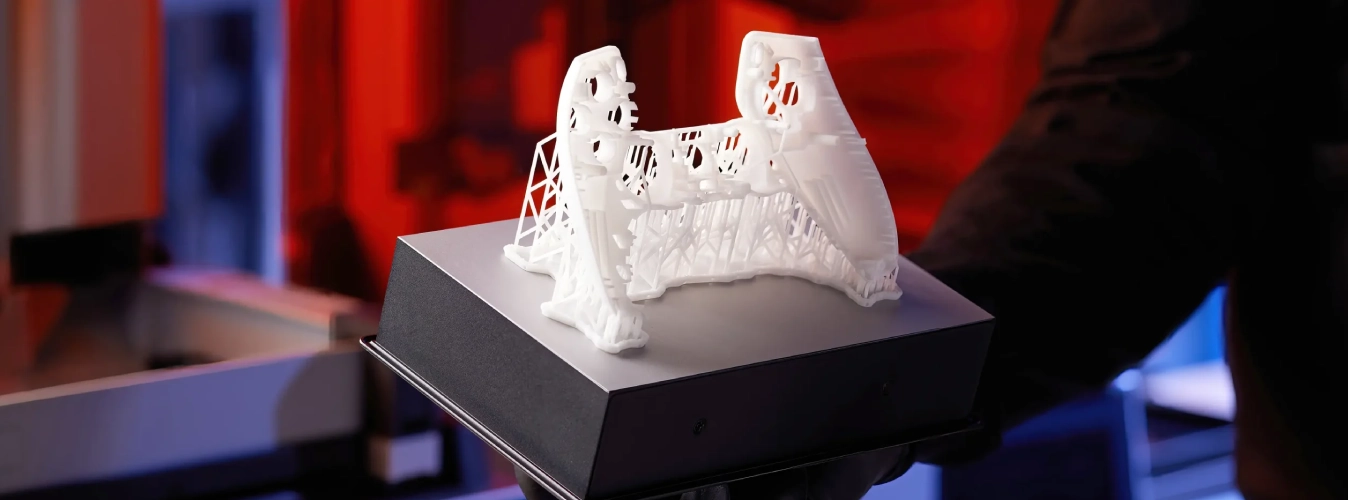
Formlabs Form 4: Velocidad, precisión y fiabilidad
El fabricante estadounidense Formlabs ha sacado al mercado una impresora 3D que está desafiando los
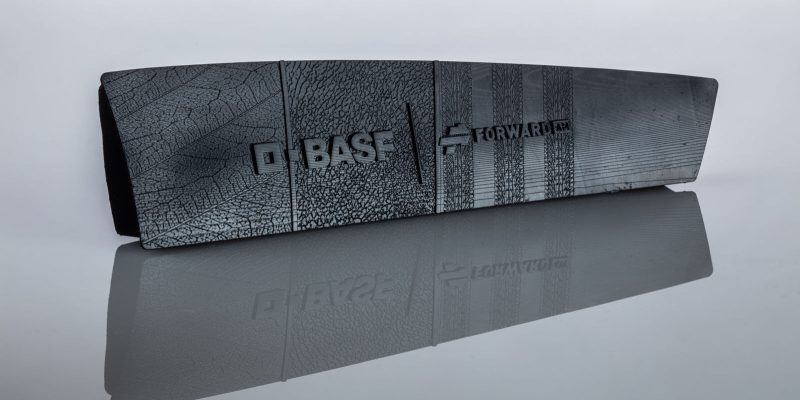
¿Qué se puede fabricar con resina para impresora 3D?
La materia prima más conocida para utilizar impresoras 3D industriales son las bobinas de filamento